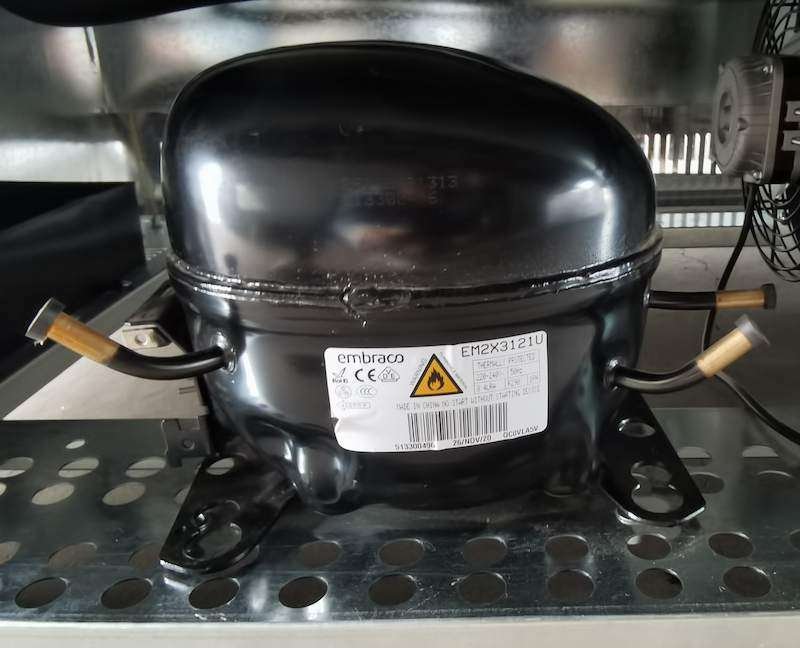
Gewerbekühlung Der Kompressor ist das Herzstück aller Kühleinheiten in Kühlschränken. Der Kompressor ist für die Zirkulation des Kühlmittels im Kühlsystem verantwortlich.
Analyse der wichtigsten Fehler und Ursachen des Kompressors, der in gewerblichen Kühlschränken verwendet wird:
1. Festgefahren: Der Kompressor ist unbeweglich und gibt ein „summendes“ Geräusch von sich:
- Eindringende Fremdkörper führen dazu, dass bewegliche Teile wie Kurbelwelle, Kolben, Zylinder usw. stecken bleiben.
- Druckungleichgewicht auf der Hoch- und Niederdruckseite.
- Durchgebrannter Motor.
- Niederspannung.
- Dem Kompressor fehlt Öl oder er wird überlastet, was zu starkem Verschleiß mechanischer Teile führt.
- Ölverschlechterung, die zu starkem Verschleiß mechanischer Teile führt.
- Bei Niedertemperaturheizung ist die Temperatur des Kompressors zu niedrig.
- Beschädigung oder Zerfall des Kompressorkondensators.
- Schlechter Abstand zwischen den festen Rotoren.
2. Der Kompressor kann arbeiten, aber der Abgasdruck ist niedrig:
- Kompressor saugt Flüssigkeit an.
- Fehlfunktion des Kondensators.
- Beschützeraktion.
- Hoher Widerstand in der Rohrleitung.
3. Der Kompressor kann zwar betrieben werden, schaltet sich jedoch aufgrund der steigenden Stromstärke allmählich ab:
- Beschützeraktion.
- Saugdruck ist zu hoch.
- Mechanische Teile des Kompressors sind beschädigt.
4. Kompressor-Überstrom:
- Verstopfung des Kühlsystems.
- Überlasteter Betrieb (Kältemittelmenge, Spannung).
- Lüftermotordrehzahl (Kondensatorzerfall, Lüfterstörung).
- Bei Maschinen mit variabler Frequenz muss besonders auf Steuerungsfehler geachtet werden.
- Dreiphasenmaschine arbeitet mit fehlender Phase und Wicklungsdurchbruch. Wenn Sie einen externen Überlastschutz verwenden, messen Sie mit einem Multimeter, ob der Überlastschutz leitet; im Normalzustand leitet er.
5. Lautes Geräusch:
- Wenn der Kompressor startet, kann es aufgrund einer Systeminstabilität innerhalb von 3 bis 5 Minuten zu lauten Geräuschen kommen.
- Vibrationsgeräusche von Rohrleitungen, Motor- und Lüfterflügelgeräusche, Resonanzgeräusche von Blechen.
- In das System einströmende Luft verursacht Luftstromgeräusche.
- Verunreinigungen oder Kupferspäne im System führen zu Geräuschen, die beim Auftreffen des Metalls auf die Ventilplatte entstehen.
- Schlechter Abstand zwischen den festen und rotierenden Rotoren.
- Mangel an Kältemaschinenöl.
- In den Kompressor eintretendes flüssiges Kältemittel verursacht eine hydraulische Kompression.
6. Beschädigte Ventilplatte (keine Saug- oder Druckfähigkeit, Hoch- und Niederdruck-Mischgas):
- Großer Spalt oder Feststecken zwischen den Ventilplatten (Rotationstyp).
- Kurbelwellenbruch, keine Drehung.
- Federbruch.
- Dem Kompressor fehlt Öl, übermäßiger Verschleiß der Ventilplatten.
- Fremdkörper gelangen in den Kompressorzylinder.
- Aus dem Vierwegeventil tritt Gas aus.
- Mangel an Kühlmittel.
- Eine Umkehrung der dreiphasigen Stromversorgung kann zu einer Umkehrung des Kompressors führen.
- Übermäßige Feuchtigkeit führt zu einer Eisblockade.
7. Großer Wicklungsstrom:
- Überprüfen Sie, ob andere Komponenten des Systems (hauptsächlich Motor und Steuerung) ordnungsgemäß funktionieren.
- Statordurchbruch (Spulenkurzschluss, Überlastung, fehlender Phasenbetrieb, Kältemittelleck).
- Eine übermäßige Kältemittelbefüllung kann zu einem hohen Wirkungsgrad führen.
- Überprüfen Sie, ob das System möglicherweise blockiert ist und dadurch Hoch- bzw. Niederdrucksituationen entstehen.
- Überprüfen Sie die normale Funktion des Kondensators.
- Hohe Umgebungstemperatur.